BMF Introduces microArch™ S230: The Most Advanced, Highest-Resolution Microscale 3D Printer Available
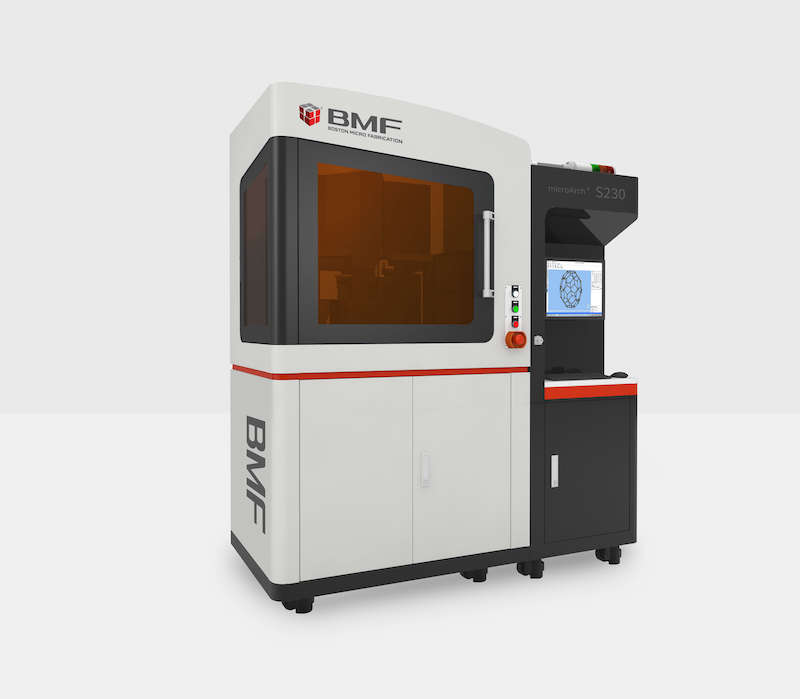
The Next-Gen Printer Combines Ultra-High Resolution With Unmatched Accuracy, Precision, and Speed for Prototyping through Short-Run Production
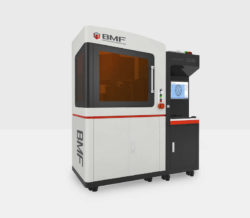
microArch S230
Boston Micro Fabrication (BMF), the pioneer in microscale 3D printing systems, today unveiled the microArch™ S230, the latest addition to its roster of industrial-grade micro-precision 3D printers. This next generation version of BMF’s highest resolution system is designed for applications that require ultra-high resolution prints (down to 2μm) with accuracy, precision and speed.
The microArch S230 brings unprecedented design freedom and part resolution to researchers and manufacturers needing micro parts with tight tolerances from prototyping through production. The printer is built upon BMF’s patented Projection Micro Stereolithography (PµSL) technology, a technique that allows for rapid photopolymerization of an entire layer of liquid polymer using a flash of UV light at micro-scale resolution, but with a larger build volume (50x50x50mm) and up to 5 times faster prints than previous models in the 2μm series.
Additional key features of the microArch S230 include active layer leveling, automated laser calibration and the capacity to handle higher molecular weight materials with viscosities of up to 20,000 Cp, resulting in the production of stronger functional parts. The printer is compatible with a growing portfolio of engineering and ceramic resins suitable for end-use parts, including three new materials being announced with today’s launch:
- AL (Alumina) Ceramic – A biocompatible and chemical-resistant ceramic resin meant for high temperature, high strength and high stiffness applications such as tooling (injection molding), casing and housings and medical devices.
- HT 200 – A durable, high-temperature and high-strength resin that can be soldered, and designed for end-use in electrical connectors and electrical components.
- MT (Magnesium Titanate) Ceramic – The combination of high dielectric constant and low dielectric loss make MT Ceramic suitable for millimeter wave applications such as antennas, wave guides and other electronic components.
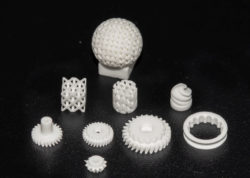
Parts printing in Alumina Ceramic
“As a current BMF customer, we’ve been thrilled with the performance of our microArch S130 to support our work in micro-printing ceramics – providing the resolution, accuracy and precision necessary for our parts. As the first customer of the new microArch S230, the next generation 2µm system, we are excited to utilize the enhancements of the platform to increase our part capacity with the larger build volume and speed up our printing times. We are looking forward to continuing to work with the BMF team and their line of micro-precision 3D printers to support our micro part needs,” said Toby Schaedler, Manager, Architected Materials and Structures Department at HRL Laboratories, LLC.
BMF launched its microArch system globally in February 2020, just weeks shy of the pandemic, and has installed over 125 units around the world. Demand continues to skyrocket as the superior production of intricate, exact, and replicable parts makes PµSL optimal for end-use and prototyping use cases across industries that were once left out of the additive manufacturing landscape, including medical device manufacturing, microfluidics, MEMS, biotech and pharmaceuticals, electronics and electrical connectors, and research and development.
“The miniaturization trend continues to dominate nearly every industry, but as parts get smaller, they become harder to design, more expensive to manufacture, and generally more complicated to put into production. Not to mention, technological barriers had previously made additive manufacturing out-of-reach for most use cases requiring small parts,” said John Kawola, CEO of BMF. “We changed that notion and brought 3D printing to industries that once deemed it impossible, and this new addition to our portfolio – the most advanced of our highest-resolution printers yet – will open even more doors for new applications on the smallest scale.”
For more information about the microArch S230 and BMF’s three newest materials, please visit www.bmf3d.com.
About BMF – Boston Micro Fabrication
Boston Micro Fabrication (BMF) specializes in micro precision 3D printing. The company’s microArch system uses a 3D printing approach called PμSL (Projection Micro-Stereolithography) that leverages light, customizable optics, a high-quality movement platform and controlled processing technology to produce the industry’s most accurate and precise high-resolution 3D prints for product development, research and industrial short run production. The technology represents a true industry breakthrough by empowering product manufacturers to capitalize on the benefits of 3D printing without sacrificing quality or scale.
Founded in 2016, BMF has offices in Singapore, Boston, Shenzhen and Tokyo. For more information on BMF please visit www.bmf3d.com or follow the company on Twitter at @bmf3d.